Introduction:
Jewelry has been a symbol of adornment and personal expression for centuries, reflecting the creativity and craftsmanship of artisans. While we often appreciate the final product, the process behind creating these exquisite pieces is equally captivating. In this blog post, we'll delve into the fascinating world of jewelry making, uncovering the meticulous techniques, dedication, and passion that go into crafting these wearable works of art.
Design Inspiration and Sketching:
The journey of jewelry making begins with a spark of inspiration. Designers draw inspiration from various sources – nature, architecture, history, culture, and more. Once an idea takes shape, designers sketch their concepts on paper, capturing the essence of the piece. These sketches lay the foundation for the piece's overall look and style.
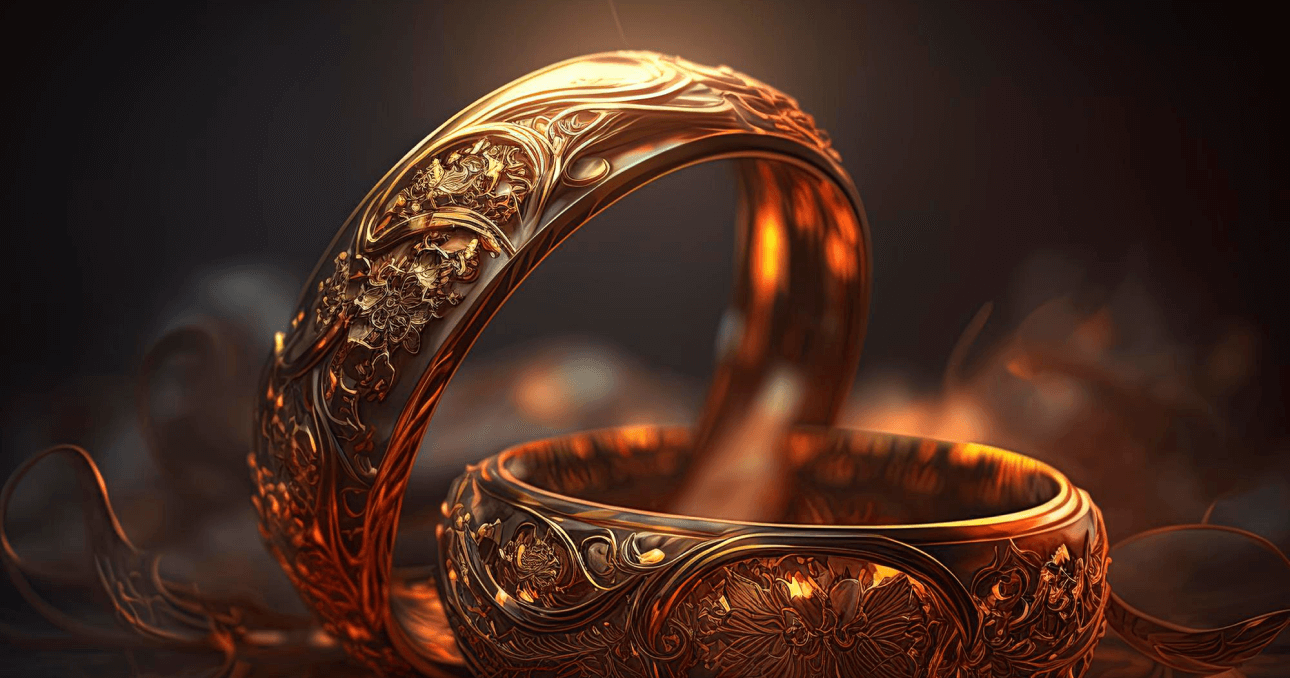
Choosing the right materials is crucial in jewelry making. Designers consider factors like the type of metal (gold, silver, platinum), gemstones (diamonds, emeralds, sapphires), and any additional embellishments. Each material has its unique properties and characteristics that contribute to the final piece's aesthetic and durability.
Wax Carving or Computer-Aided Design (CAD):
Depending on the complexity of the design, artisans may create a wax carving by hand or use computer-aided design (CAD) software to digitally model the piece. Wax carving involves sculpting the design in wax, allowing for intricate detailing. CAD, on the other hand, enables precise measurements and adjustments before moving to the actual production stage.
- Casting is the process of turning the wax model into metal.
- The wax model is encased in a plaster-like mold, and the wax is melted away, leaving behind a negative space.
- Molten metal is then poured into the mold, taking on the shape of the original wax model.
- Once cooled and solidified, the metal piece is removed from the mold.
- The cast metal piece often requires refinement.
- Jewelers use various tools to file and shape the piece, ensuring smooth edges and perfect contours.
- ordering is employed to join different metal components, like attaching clasps or setting mounts for gemstones.
- This stage demands precision and skill to achieve seamless connections.
Stone Setting:
Gemstones are carefully set into the piece using specialized techniques. Prong settings, bezel settings, and pavé settings are some examples. Stone setters secure each gemstone, ensuring they are secure and aligned according to the design. This delicate process requires steady hands and a keen eye for detail.
Polishing and Finishing:
Polishing brings out the shine and luster of the metal. Jewelers use polishing compounds and tools to achieve the desired finish – from high-gloss to satin. This step adds the final touch to the piece, enhancing its visual appeal.
Quality Control:
Before the jewelry piece reaches the customer, it undergoes thorough quality control. Experts inspect the piece for any imperfections, ensuring that it meets the highest standards of craftsmanship and durability.
Packaging and Presentation:
The final step involves carefully packaging the jewelry. Luxurious boxes, pouches, and certificates of authenticity are often included to provide an exquisite presentation worthy of the artistry within.
Conclusion:
The art of jewelry making is a harmonious blend of creativity, precision, and passion. From the initial spark of an idea to the final polished piece, artisans invest their skills and dedication to create wearable masterpieces that transcend time. The next time you admire a piece of jewelry, remember the intricate journey it undertook – a journey that transforms raw materials into symbols of beauty and elegance.